Quality Assurance and Quality Policy
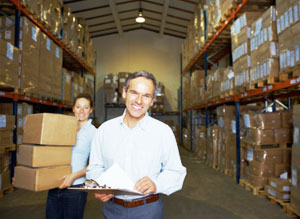
The development of NAFCO’s technical quality system initially originated from the ISO 9001 standard certification in 1998. Under the support of the instruction, cultivation, and assessment rendered by world-famous engine manufacturers, we were rated as a qualified supplier by GE and Snecma in 2001 and 2003, respectively.
Corresponding to the customer’s product requirements, NAFCO was also granted several Special Process Qualification, including chemical processing (silver plating, copper plating, chromium plating hard deposit, passivation, coating-dry film lube, titanium cleaning),
electrical discharge machining (EDM), heat treat, non-destructive testing (NDT – fluorescent penetrant inspection and magnetic particle inspection), metallurgy inspection by the Metallic Material Laboratory in respect to micro & macro metallographic inspection, hardness test, and product mechanical properties test (tensile strength, self-locking torque, stress rupture, tension fatigue, etc.).
In 2004, NAFCO introduced the AS 9100 aerospace quality system standard, the accreditation was successfully certified, and the original quality system was amended by adding extra requirements for the Aviation, Space, and other industries. The system puts special emphasis on the management of the specific quality requirements of the customer, such as the traceability of the quality records, product realization verification, configuration management, and work transfer management.
In 2005, we introduced the ISO/TS 16949 quality system. With efficient application of the five core tools, i.e., APQP, FMEA, SPC, MSA, and PPAP, for working with the processes-based method, we were able to develop the automobile market, attributing to our ability in the design and manufacturing of fasteners.
In 2005, NAFCO filed the application to secure third party accreditation, NADCAP, for the special processes as jointly required by the aerospace customers, and the chemical process, heat treatment, and non-destruction testing (NDT) certificates were granted in 2005, 2006, and 2007, respectively, which are also displayed on the NADCAP website: “Qualified Special Process Supplier List”. In this regard, NAFCO will be subject to continual auditing in order to maintain the certification qualification.
The Quality Management System of NAFCO is developed and implemented according to customer demand. Through process methodology, customer demands are incorporated in the key processes during product introduction and the manufacturing process, mutually connecting the management and support process so that all products supplied by the company can meet customer requirements and expectations. Furthermore, we also analyze the process performance through monitoring and measuring for continual improvement, so as to enhance product quality, delivery, and the cost competitiveness.
- NAFCO Quality Policy
- Management Policy:
- Customer Satisfaction:
Customer Satisfaction: Declare the “Customer Satisfaction” as the top policy, and to promote all employee always to make great efforts to achieve customer satisfaction throughout the product life cycle from development to phase-out.
- Zero Gaps of Compliance:
The Product Safety/Flight Safety commitment is the most basic ethical Code. And the fundamental code of conduct to promote Product Safety//Flight Safety is strictly follow procedures and instructions which are flowing down from applicable statutory, regulatory and customer requirements. (e.g., fraudulent, ethics, counterfeit, etc.)
- Total Accountability::
Everyone is encouraging to identify risks of both Human and Organizational factors. Under an “OPEN REPORTING” and “JUST” culture without fear of retribution. To ensure the product safety/flight safety, everyone is responsible to report any discovered human mistake / error. Continually improving the maturity of both Human Factor deployment and flight safety awareness within the organization.
- Enterprise Sustainability:
To identify risks and opportunities agonist’s internal and external issues by using of Risk-Based Thinking, and continuously improving, innovating and developing Intelligent Automation through utilization of management tools. To strengthen organizational resilience for meeting of requirements and expectations of all interested parties, and pursue sustainable business operations.
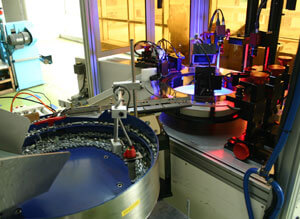
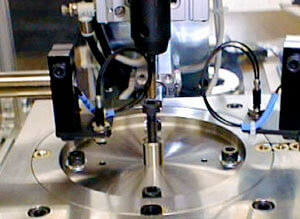
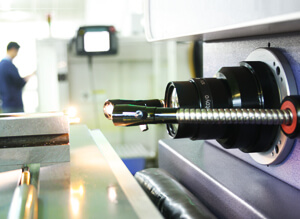